汽轮发电机组润滑油系统冲洗新方法
发布日期:2017-03-14 来源:《上海设备管理》
点击数:38316
发电机组中,作为主要设备的蒸汽轮机、燃气轮机、发电机,其安全性和稳定性直接影响机组的安全生产。根据已投产的发电机组在安装、调试、生产过程中遇到的一系列技术问题,其主要难题都围绕转子轴系,表现为振动和瓦温的异常,而这两方面都与轴承润滑油相关。汽轮机润滑油系统主要用于轴承润滑、冷却、调速和发电机氢气系统密封,在机组安装、检修过程中由于各种原因导致润滑油清洁度下降,会产生转子轴颈磨伤,轴瓦及密封瓦钨金磨损等现象,因此汽轮机油清洁度的好坏直接影响机组运行的安全可靠性。
新建机组或大修机组应进行汽轮机润滑油系统冲洗,以确保润滑油系统的清洁度,而选择何种油冲洗方式,则决定了油冲洗所需时间与效果。本文在分析传统汽轮机润滑油系统油循环冲洗方法不足的基础上,提出了采用蒸汽冲洗的新方法,并对该方法的工程实用价值进行了探讨。
一、传统润滑油系统冲洗方法
汽轮发电机组润滑油系统管道冲洗通常分两个阶段,第一阶段是润滑油不进轴承座的外部管道冲洗;第二阶段是所有正式润滑油系统管道内循环冲洗。新建机组的润滑油系统管道冲洗通常需要完成这两个阶段冲洗,而投运机组大修后或停运中冲洗则往往仅需完成第二阶段工作即可。第一阶段外部管道冲洗,通常不包括润滑油正式系统的油泵设备,而需采用临时的大流量油泵并配套部分临时管道。这个阶段的冲洗是机组安装调试过程中的关键环节,也是被认为最不可控制的阶段,只有第一阶段冲洗油质验收合格,才能进入第二阶段的正式油系统内循环。第二阶段是正式油系统全部投运,轴承箱进油,系统进行泵内循环运行,对于所有机组来说,工作流程基本一致。因此如何提高第一阶段的油系统冲洗效果、缩短冲洗时间,是新建发电机组安装调试及运行管理工作的重点问题。
对于润滑油系统第一阶段外部管道冲洗,研究文献很多,传统的方法多是采用油或水作为介质冲洗。最为常见的是应用润滑油作为冲洗介质,采用交替变油温冲洗工艺,依靠油循环的连续冲刷力及温度变化产生的热应力带走系统及管道内的遗留杂质,但是所有杂质依然靠润滑油排油或者滤网清理时才能去除,工作耗时耗力,尤其是冲洗初期,杂质多,工作量大,且整体冲洗效果欠彻底,图1为第一阶段采用大流量油循环冲洗的工艺流程。
图1 润滑油系统第一阶段冲洗工艺流程
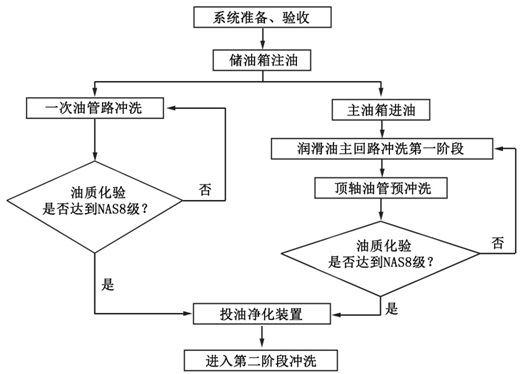
其次是采用水洗或者酸洗冲洗工艺进行油管道冲洗,使用水基液体作为冲洗介质,能够一次性带走管道内的杂质,且不需要进行反复的人工清理,冲洗效果能满足要求,但是酸洗会带来额外的二次污染及环境污染。同时,临时系统也相对复杂。
二、润滑油系统冲洗新方法
为了改进润滑油冲洗的第一阶段工艺,需采用新的冲洗方法。新的冲洗方法需要解决两个关键问题:一是能使管道杂质能一次性彻底地从管道系统中去除;二是能使管道内壁粘附的杂质及制造残留物等快速脱落剥离。解决好这两个问题,第一阶段的油冲洗时间将会大大缩短,冲洗效果也会大幅改善并能保持长久稳定状态,进而确保第一阶段的油冲洗过程可控。
针对第一个问题,可以通过提高冲洗能量入手;第二个问题可以通过增大管道冷热交替变化的工况来实现。借鉴新建机组锅炉及主蒸汽管道的蒸汽吹扫经验,采用低压蒸汽作为冲洗介质,对润滑油管道进行冲洗,考虑到润滑油系统管道的设计承受压力和运行工况,选定恰当的冲洗蒸汽参数,制定相应的暖管、冲洗、冷却、再冲洗的冲洗工艺,提出润滑油管道系统蒸汽冲洗的新方法。
利用该方法,针对某1000MW汽轮发电机组开展润滑油管道系统蒸汽冲洗新方法的应用实践。如图2所示,该1000MW汽轮发电机组润滑油系统采用模块化设计,由润滑油箱、交流润滑油泵、直流润滑油泵、顶轴油泵、排烟风机、电加热器、冷油器和双联过滤器等设备组成,从汽轮机方向看油管路为右侧布置。润滑油泵直接从油箱吸油,润滑油经过滤油器、冷油器及节流阀供至各个轴承,每个轴承的润滑油量可通过节流阀进行调整。
图2 某型汽轮发电机组的轴系润滑油系统
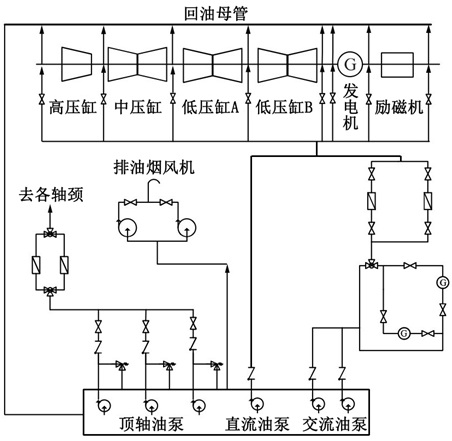
结合机组管道布置形式,设计了辅助蒸汽冲洗临时管道系统。如图3所示,采用接临时蒸汽管道至润滑油油泵出口供油管道及回油管道,同时在轴瓦进油处及回油处采用管道短接至冲洗排放母管,冲洗完毕的蒸汽对空安全排放(接一根直径219mm的临时冲洗排放管至17m窗外对空排放)。就近采用邻机或其它辅助系统的低参数蒸汽,结合机组实际情况,蒸汽参数选择控制为压力0.8~1.0MPa,温度280~300℃。
图3 润滑油冲洗系统
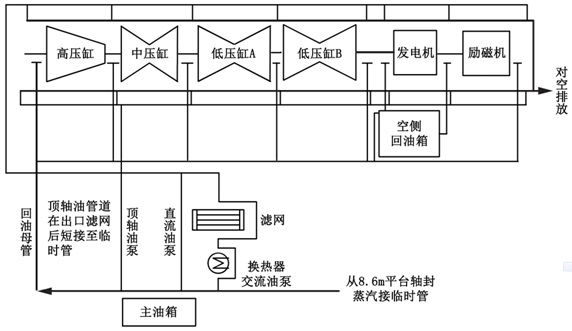
具体冲洗操作步骤如下:
(1)临时管道系统安装及检查验收。
(2)冲洗蒸汽从8.6m平台处通过临时管道从润滑油泵及顶轴油泵出口处接入润滑油管道系统,进入汽轮机平台润滑油母管,然后通过临时管道排出,回油管道采用逆向冲洗的方式。
(3)在系统蒸汽冲洗前,应进行充分疏水、暖管,避免冲洗时管道发生剧烈振动;同时检查整个冲洗系统是否存在泄漏,若有则需消除后再继续。
(4)暖管结束后,第一次进行试吹,缓慢提高冲洗蒸汽压力至设定值,同时检查系统是否正常。
(5)正式冲洗。每次蒸汽冲洗时间为10~15min,冲洗间隔时间为5~10min,冲洗次数一般3~5次即可,最终视排放口汽水干净为止。采用这种反复间隔冲洗和冷却的方法,有利于管道杂质脱落,通过蒸汽带走。
(6)冲洗结束后临时管道的恢复,对于系统部分死角,采用人工清理即可。
三、冲洗新方法效果及优点分析
1、冲洗效果分析
对机组实际冲洗效果进行分析,与传统的冲洗方法相比,蒸汽冲洗在冲洗时间、冲洗结果、蒸汽对管道的影响等方面都具有显著的优势。
(1)冲洗时间方面,汽轮发电机组润滑油系统采用辅助蒸汽为汽源的开放式冲洗工艺,显著缩短了润滑油管道系统第一阶段的冲洗时间,加快了机组润滑油系统整体冲洗周期,提升了机组进入整套启动试运的时间,缩短了机组整体安装调试工期,对比于传统大流量油循环冲洗工艺能够节省5天时间。
(2)冲洗结果方面,对系统冲洗完毕后充油试运后的油质进行第三方检测,表1为检测报告给出的冲洗完毕后100mL油样中不同粒径范围的颗粒数,按照美国航空航天工业联合会发布的NAS1638标准,各个评价指标优秀,颗粒度标准为NAS4级,明显优于常规同类机组采用油循环冲洗的NAS7级结果。
表1 润滑油油质报告
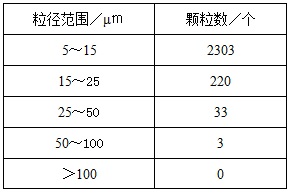
(3)对蒸汽冲洗后的管道进行金相分析,结果表明:试验样品微观组织未产生变化,不会对后期使用产生安全隐患。
2、冲洗优点
通过在某台1000MW汽轮发电机组润滑油系统管道蒸汽冲洗中的实际运用,与传统大流量油循环冲洗方法的效果对比,该方法具有以下优点:
(1)管道杂质清理彻底,油质颗粒度标准高,冲洗效果好。
(2)节省系统冲洗时间,缩短了整台机组安装调试工期,有助于机组按期投产。
(3)节省大量冲洗用油,节约了耗油量。
(4)规避了酸液使用,减少了脏污油液的产生,有效缓解了处理污油及酸液的环境危害压力,环保效果好。
四、结论
本文在分析传统汽轮机润滑油系统大流量油循环冲洗方法不足的基础上,提出了采用蒸汽冲洗的新方法,阐述了具体的技术路线和实施步骤,采用压力为0.8~1.0MPa,温度280~300℃的辅助蒸汽作为冲洗介质,在某1000MW汽轮发电机组的基建调试过程中,开展了工程实践应用,结果表明蒸汽冲洗新方法具有环保、省时、省油、冲洗效果好等优点,对同类新建机组安装调试工作具有很好的借鉴参考作用。
作者:潘克坚 单位:上海电力建设启动调整试验所